Equipment
Pesticide application equipment varies widely from the simple paintbrush,
plunger duster, pressurized can or aerosol bomb to the modern agricultural
airplane that is fully equipped with liquid spray systems and/or granular
spreaders. There are also several types of support equipment filler pumps, tank
trucks, nurse or mixing tanks, front-end loaders, etc. that are not used in
actual application but that make the spray operation more efficient.
Would you like to try a study question?
Goals of This Module
- Learn the names and uses of the various types of application equipment.
- Learn how to select the best application equipment for the job.
- Understand the basic principles of operation for each type of equipment.
- Know the advantages and disadvantages of each type of application equipment.
Choose Your Equipment Wisely
Most application equipment can be used for several different kinds of problems.
By choosing the type of equipment best suited for his type of work, the
applicator can save himself and his customers time and money. The aerial
applicator's equipment differs greatly from that of the structural pest control
operator. The arborist uses machinery suited for arborist needs. Even when he
specializes in a specific type of pest control the pesticide applicator will
need to make a choice of equipment. The choice will depend on his working
conditions, pesticide formulation, type of area treated, possible problems, etc.
While large power equipment may be desirable for some problems, other jobs may
be best done by using small portable or hand equipment. Most application
equipment can be placed into two groups; one group that applies dry pesticide
formulations and another for liquid pesticides.
Would you like to try a study question?
Dry Formulation Equipment
Dusters
Dusters blow fine particles of pesticide dusts onto the target surface. They may
be very simply constructed. Often the package containing the pesticide dust acts
as the duster, such as a plastic squeeze bottle or a telescoping tube with a
spout. Even the larger powered models are of simple construction. Dusters are
used mostly by home gardeners, pest control operators, and truck gardeners for
individual spot treatment of plants or a small area. In some areas dusts are
still applied with aerial application equipment.
Advantages.Dusters are lightweight, relatively cheap, and fast acting.
They do not require water.
Disadvantages. Dusts are highly visible, drift easily and are difficult
to control. Because of this, dusters are less desirable for most crops or large
outdoor jobs.
Would you like to try a study question?
Granule Spreaders
Granular equipment is designed to apply coarse, dry particles that are uniform
in size to soil, water, and in some cases foliage. Spreaders may work in several
different ways including pneumatic whirling discs (seeders, fertilizer
spreaders), multiple gravity feed outlets (lawn spreaders, grain drills), soil
injectors (furrow treatments), and ram-air (agricultural aircraft).
Advantages. Granular equipment, like dusting equipment, is light,
relatively simple, easy to calibrate, and no water is needed. Because granules
are uniform in size, they flow easily and are relatively heavy. Seeders and
fertilizer spreaders can be used to apply pesticide granules, often without
modification.
Disadvantages. Granular formulations have a limited number of uses and
are known to poison non-target wildlife if left uncovered. Therefore, the
applicator will need other machinery for controlling most leaf feeding insects
and plant diseases.
Would you like to try a study question?
Would you like to try a study question?
Liquid Formulation Equipment
Sprayers
More pesticides are applied with sprayers than with any other equipment.
Consequently, there are many different types and sizes of sprayers varying from
hand operated units to machines weighing several tons. Some apply dilute
pesticide mixtures while others apply concentrates. Some use low pressure and
low gallonage (low volume) and usually have simple roller pumps. Others are high
pressure and/or high volume, usually supplied by high pressure piston pumps.
Some apply spray through single outlets or nozzles while others use multiple
nozzles linked by sections of pipe or tubing to form a boom. The principal types
are described below but there may be several variations or combinations of these
types.
Hand Operated Sprayers
Hand operated sprayers are most commonly used by individuals for their own
relatively small pest problems. However, the commercial applicator will often
find it convenient and efficient to have hand sprayers for small jobs that do
not require larger powered equipment or that require only a small amount of
spray. They are also used for small jobs in hard-to-get-at areas where the spray
equipment must be carried in. Hand sprayers use carbon dioxide or compressed air
to force the spray liquid through a nozzle. These sprayers may be available for
use with single or multiple nozzle systems. The capacity of hand sprayers
generally ranges from one-half to five gallons.
Advantages.Hand sprayers are economical, uncomplicated, light-weight,
yet will do a surprising amount of work and adapt to many different problems.
The spray is easily controlled when it comes to direction, drift, etc., because
relatively little spray is used at low pressure.
Disadvantages. Hand sprayers are efficient and practical for small jobs
only. Wettable powders tend to clog regular nozzles and agitation is frequently
poor.
Would you like to try a study question?
Would you like to try a study question?
Low Pressure Boom Sprayers
These sprayers are usually mounted on tractors, trucks, or trailers. They are
designed to be driven over field crops or large areas of turf, applying the
pesticide in swaths. Low pressure sprayers generally use a relatively low volume
of dilute spray ranging from 10-40 gallons per acre and applied at 30-60 psi.
Typical low pressure sprayer components consist of a pump, tank, agitation
system, flow control valves and the boom. Low pressure sprayers use roller or
centrifugal pumps.
Advantages. Low pressure sprayers are relatively inexpensive,
lightweight, adapted to many uses and can cover large areas rapidly. They are
usually low volume, so one tankful will cover a large area.
Disadvantages. They will not adequately penetrate and cover dense foliage
because of their low capacity (pressure and gallonage). Because most use
hydraulic agitators, wettable powder formulations often settle out. However, if
mechanical agitators are used the problem is solved.
Would you like to try a study question?
Would you like to try a study question?
High Pressure Sprayers
High pressure sprayers are often called "hydraulic sprayers." They operate with
dilute mixtures and different pressures from two hundred and fifty up to several
hundred psi. The design of high pressure sprayers is similar to that of low
pressure sprayers, the only difference being that the components have to
withstand high pressures. When fitted with booms they can do any work done by a
low pressure boom sprayer. They may also be fitted with handguns. The handguns
are used for spraying shade trees and ornamentals, livestock, orchards,
buildings, unwanted brush, rights-of-way, commercial crops, etc.
Advantages. High pressure sprayers are useful for many different pest
control jobs. They have enough pressure to drive spray through heavy brush,
thick cow hair, or to the tops of tall shade trees. Because they are strongly
built, they are long lasting and dependable. Piston pumps are standard and
resist wear from gritty or abrasive materials. Mechanical agitators are also
standard and keep wettable powders well mixed in the tank. With a long hose,
targets in hard-to-get-at places such as trees, shrubs, etc., can be treated. If
label directions for mixing are followed the applicator is not likely to
overdose.
Disadvantages. High pressure hydraulic sprayers have to be strongly built
and can be heavy and costly. They usually use large amounts of water and thus
require frequent filling. The pesticide can easily be misdirected, causing drift
and off-target contamination.
Would you like to try a study question?
Would you like to try a study question?
Air Blast Sprayers
Air blast sprayers use air and water to deliver the pesticide to the target
surface. The pesticide mixture is pumped through a nozzle or a series of
nozzles. A high performance fan (blower) creates an air blast that blows the
pesticide away from the spraying nozzle. The rushing air shatters the liquid
into tiny droplets that are carried to the target by the air blast. The high
speed air aids in breaking up larger droplets and transporting the smaller
droplets for thorough coverage. The droplets may be carried 10 to 40 feet
effectively depending on the need and the fan speed. Air blast sprayers are
typically used in operations involving tree spraying, but are also used in field
crop situations where the air blast provides a more effective means of
penetrating foliage and providing coverage on all parts of plants.
Advantages. A small amount of pesticide mixture covers a large area and
little operating time is lost in refilling. They are usually less tiring to
operate than hydraulic sprayers and are particularly adapted to applying sprays
over a large area in a relatively short time. They provide an effective means of
delivering pesticide to hard-to-reach areas and through dense foliage.
Disadvantages. Air blast sprayers are relatively expensive machines.
Since the pesticide is carried by an air blast, they must operate under calm
conditions. Windy conditions interfere with the normal pattern of application of
the blower. Wind can also cause the small, fine particles of concentrate to
drift into surrounding areas where they may do damage. The visible mist that is
blown into the air gives the perception that pesticides are missing the target.
Larger models may not be able to treat hard-to-get-at areas.
Would you like to try a study question?
Would you like to try a study question?
Low, Ultra-low Volume Sprayers, and Volume Air Sprayers
ULVs and mist blowers
Mist blowers use a fan or whirling disk to break up and blow spray droplets
toward a target. Both units apply low volumes of pesticide on target in the form
of a mist. The mist consists of small droplets and is often hard to see. These
sprayers depend on a metering device, which may or may not be a conventional
nozzle. Low volume mist blowers use a diluted pesticide mixture, but ULV mist
blowers use undiluted concentrate.
Advantages. Saving time and labor is the main advantage of low and ultra-low
volume sprayers. This is accomplished by limiting the amount of liquid carried.
These devices are light weight and easy to use. Effective pest control is
achieved with a minimum of liquid applied, thus eliminating the problems with
wet, dripping walls, animals or plants.
Disadvantages. Calibration is critical and overdosing is a potential problem
because the applicator is applying a concentrate or nearly concentrated
pesticide. Applying pesticides in favorable weather becomes more critical with
this equipment than with air blast sprayers. A more concentrated mixture is
being applied and drift could have devastating effects. Coverage with very low
volumes on some crops may be less effective and thus less control is achieved.
The use of concentrated pesticides increases the risk to the applicator. There
are only a limited number of pesticides labeled for ULV application at the
present time.
Aerosol Generators
Foggers
Aerosol generators break certain pesticide formulations into very small, fine
droplets (aerosols). An individual droplet cannot be seen with the naked eye.
When large numbers of droplets are formed, they can be seen as a fog or smoke.
This is why the machines are commonly called "foggers." In some foggers, heat is
used to break up the pesticide. These are called thermal aerosol generators.
Other foggers break the pesticide into very fine particles with rapidly whirling
discs, air blast breakup, or extremely fine nozzles. Aerosol generators are
usually used to completely fill an area with a pesticidal fog, whether it be a
greenhouse, warehouse, or open recreational grounds. Insects and other pests in
the treated area can be controlled when they come in contact with the aerosol
fog.
Advantages. The droplets produced by foggers are so fine they do not
stick to surfaces within an area. Therefore, foggers can be used in the home for
flying insects, in commercial buildings for a variety of pests, or outside in
populated areas for blackflies and mosquitoes without leaving unsightly
residues. The droplets float in the area and penetrate tiny cracks and crevices
in furniture or through heavy vegetation to reach pests in hard-to-get-at
places. Because they blanket an area, it is difficult for pests to escape
exposure.
Disadvantages. Since most of the droplets produced by aerosol generators
do not stick, little residual control of a pest is possible. As soon as the
aerosol moves out of an area other pests can move back in. Also, the droplets
produced are so fine that they drift for long distances and may cause unwanted
contamination or injury. Most aerosol generators require special pesticide
formulations. A general purpose formulation usually is not suitable. When
foggers are used outside, the weather conditions must be just right. For
example, if an area is being treated for mosquitoes, rising air currents could
carry the aerosol harmlessly over the pests and out of the area. There must be
little or no wind, otherwise the pesticide may be flushed from an area before it
can be effective. When a building or an area is treated, it should be ventilated
before it can be reoccupied to avoid harmful exposure to the pesticide.
Would you like to try a study question?
Would you like to try a study question?
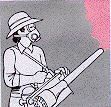
Pumps
Flexible-Impeller pumps. Flexible-impeller pumps have a series of rubber
"paddles" attached to a rotating hub. The pump housing is eccentric in shape and
squeezes the paddles as the rotor turns. This pump has an automatic pressure
relief characteristic. The paddles will not return to the radial position if the
pressure is to high. The pump is limited to low pressures (less than 50 psi) and
can handle all except highly abrasive materials.
Would you like to try a study question?
Roller pump. Roller pumps are probably the most widely used pump because
they are effective, flexible and inexpensive. The "rollers" of a roller pump fit
into slots of a rotating hub. The slots allow the rollers to follow the
eccentric shape of the housing. As the rollers pass the inlet port, they push
the liquid around the housing and toward the outlet port. As the rollers near
the outlet port, the spaces become smaller and fluid is pushed out. The output
from a roller pump decreases as the pressure increases because the rollers leak
back fluid between rollers. Roller pumps are easily and economically rebuilt
when worn.
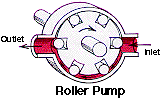
Centrifugal pumps. Centrifugal pumps have become increasingly popular in
recent years. They handle abrasive materials well and their high capacity
provides plenty of hydraulic agitation. This pump has an automatic pressure
relief characteristic. One of the limitations is that they must be driven at
high speed to develop pressure. Belt, gear, or hydraulic drives are used to gear
up the pump to high speed. This pump requires priming unless it is located below
the level of the supply tank. Pump output falls off rapidly at 30 to 40 psi. The
steep performance curve is an advantage as it permits controlling pump output
with a relief valve. However, it also produces uneven pump output under some
conditions.
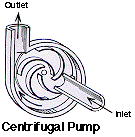
Piston pumps. Pistons are "positive displacement" pumps, which means that
every time the piston moves the liquid must move. There is no leakage inside the
pump chamber or automatic pressure relief characteristic like the roller pumps
have. The piston pump output is virtually unaffected by pressure. Pump output is
usually low and may not be sufficient for hydraulic agitation. It is the most
expensive pump, but good for wettable powders and other abrasive mixtures.
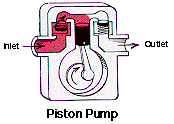
Gear pumps. The gear pump is a semi-positive displacement type of pump
and was used on many early sprayers. Gear pumps are rarely used today because of
the high wear rate that occurs when pumping abrasive fluids. It is well suited
to pumping oil suspensions or emulsions at high volumes and pressures. The
internal parts (housing and gears) are generally made of bronze and the shaft is
made of stainless steel. The pump cannot be rebuilt and must be thrown away when
it is worn.
Diaphragm pumps. The pumping action in a diaphragm pump is produced by
moving a flexible diaphragm. Liquid is drawn into one chamber on the downstroke
and forced out of another on the upstroke. These pumps may be constructed with
either one or two diaphragms. The diaphragm is resistant to wear from abrasives,
but may be worn by certain chemicals. Diaphragm pumps are moderately priced and
servicing is easy and economical.
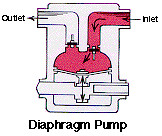
Ground driven pumps. Ground driven pumps, or metering pumps, are powered
by a ground wheel. When speed changes, the rate of pumping changes accordingly.
The major advantage of these pumps is that the application rate is held constant
as the speed changes, compensating for changes in terrain and surface
conditions. There are two types of pumps normally used on sprayers with ground
drives.
Would you like to try a study question?
The variable-stroke piston pump is designed to change the length of the
piston stroke to adjust the application rate. Increasing piston stroke increases
flow; reducing stroke cuts flow. When driven by a ground wheel, the applicator
selects a flow rate by setting the piston stroke. Once the flow rate is selected
it will stay the same whether the sprayer is traveling one mph or five mph.
The hose pump consists of a series of rollers on a reel with a flexible
hose stretched over the reel. As the ground wheel drives the reel, the rollers
push a fixed amount of fluid around the hose, thus pumping the fluid. Flow from
this pump cannot be changed.
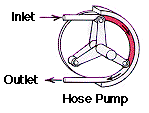
Sprayer Nozzles
Nozzles for sprayers are very important to proper pesticide application. Even
experienced applicators often overlook the proper selection and maintenance of
nozzles, perhaps the most important component of liquid pesticide application
equipment. You as a new candidate for applicator certification must realize from
this point on that with improper or worn nozzles, accurate application can never
be utilized.
Nozzles (often called "spray tips") serve three functions:
- Meter or regulate the flow of the liquid
- Atomize the liquid stream into droplets
- Spread droplets in a specific pattern
Would you like to try a study question?
Regulate flow. A nozzle regulates the flow of liquid with the size of
it's orifice. The pressure of the liquid is also a factor. With most nozzles,
flow rate increases as pressure increases. However, doubling the pressure
does not double the flow rate. Pressure must be increased four times to
double the flow rate.
Would you like to try a study question?
Atomize stream. Atomization of a liquid into droplets is caused by the
tearing action of air. The nozzle spreads the liquid into a thin unstable sheet
which breaks up into droplets as it hits the air. Each nozzle produces a range
of droplet sizes from very small to large. Droplet size is measured in microns
one micron is equal to one millionth of a meter. An increase in the pressure
causes an increase in tearing action, thus the droplets become smaller. If the
droplets are too small drift will become a problem. If droplets are to large
they will not stick to the surface and will roll off. Droplet size is an
important consideration when selecting nozzles. Most nozzle manufacturers give
droplet size information in their catalogues.
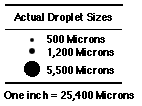
Spray nozzle tip wear. Worn nozzles have poor spray patterns and higher
flow rates than new nozzles. Determine spray tip wear by comparing the flow rate
of the used tip to the flow rate of a new one. Check the flow of each used tip
by using an accurate graduated container and collecting liquid for a measured
time. If the flow rate of the used tip is five percent greater than a new one,
it should be replaced.
Would you like to try a study question?
Would you like to try a study question?
Maintain the nozzle. Nozzles must be protected from grit and dirt by
adequate screens. Finely machined edges that control spray pattern can be
damaged by the sanding action of dirt and abrasive spray mixtures. Clogged tips
should be cleaned with a soft bristled brush only, never use a metal
object. Use extreme care with soft tip materials such as plastic and brass.
Remember!! Never put a dirty, clogged nozzle to your mouth to clean it.
Nozzle materials. Materials used to construct spray nozzles are chosen
for their cost and durability. Although other materials are in use today, the
following list gives the most common types.
- Brass - probably the most commonly used, least resistant to wear and
relatively inexpensive.
- Nylon - used for non-abrasive formulations, inexpensive and
corrosion-resistant. Not recommended for high pressure.
- Plastic (polymer) - can be used for corrosive chemicals. Different grades
of plastic available with the more expensive grades show-ing good wear
resistance.
- Stainless steel - non-corrosive, excellent wear resistance and relatively
expensive.
- Hardened stainless steel - very durable and useful for highly abrasive
formulations.
- Ceramic - most durable tip for highly abrasive and/or corrosive
chemicals.
Would you like to try a study question?
Nozzle Spray Patterns
Hollow cone and solid cone nozzles produce a circular pattern. Hollow
cone nozzles generally make finer, smaller particles than the solid cone. These
nozzles are used on handgun sprayers and row crop sprayers. They generally
penetrate foliage well and are used to apply fungicides, insecticides and
sometimes herbicides.
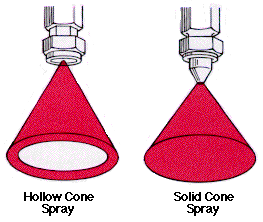
Flat spray nozzles are used to broadcast most types of pesticides. The
pattern is fan shaped with gradually tapered edges. Uniform coverage across the
sprayer width is achieved by overlapping the tapered portion of the pattern.
This is also a common spray pattern used for applying structural pesticides to
floor or wall surfaces.
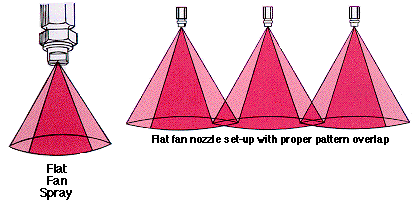
Even spray nozzles produce a narrow rectangular pattern with a sharp cut
of edges. They are used for band applications of chemicals and are frequently
used with planting equipment.
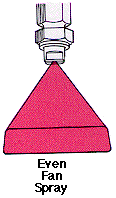
Flooding nozzles are often used for broadcast application of fertilizers,
herbicides and defoliants. They deliver a wide flat spray pattern consisting of
large droplets. They can be mounted on a boom in a variety of positions and are
sometimes used alone for boomless broadcast spraying.
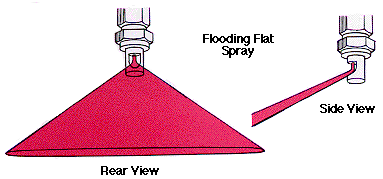
Multi-pattern spray nozzles are used on professional hand held sprayers
and usually provide the applicator with a choice of different patterns built
into one nozzle. Usually two flat fan patterns are availabl e; one that produces
fine particles and low volume patterns and a large volume fan with large
particles. Another pattern will be the pin stream, used to apply the pesticide
into a hole or crevice. There may also be a "crack and crevice" accessory tool
attached as well. The applicator selects these patterns by loosening the nozzle
collar and turning the nozzle body so that the desired pattern is used.
Would you like to try a study question?
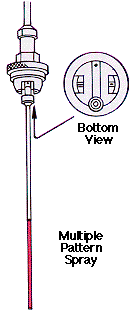
Care of Equipment
Whether equipment is very simple or very complex, it must be properly cared for
so it will be both dependable and safe. Cleaning equipment including hoses,
nozzles, pumps, tanks and hoppers is very important. Pumps and other equipment
that will be stored in below freezing weather should be thoroughly drained, or
better yet alcohol or antifreeze should be circulated through the equipment.
Nozzles should be removed, cleaned, and stored.
Cleaning Sprayers
Clean the sprayer after each days use. appropriate protective clothing when
cleaning any piece of application equipment. Flush with clean water inside and
out to prevent corrosion and accumulation of chemicals. When finished for the
season or when changing chemicals, clean the sprayer thoroughly with a cleaning
agent. Be careful to avoid contaminating water supplies and avoid injury to
plants or animals when washing.
These steps are suggested:
- Wash off the inside of the tank and partially fill it with water. Flush this
water through the nozzles. When the tank is empty repeat these steps so that two
complete rinses are done.
- Take off the nozzle tips and screens. Clean them in a strong detergent solution
or kerosene using a soft brush.
- Fill the tank a third time, this time adding a cleaning agent. Refer to the
following table for information on the type and amount of cleaning agent.
Would you like to try a study question?
Would you like to try a study question?
Cleaning Agents and Rates for Cleaning Sprayers
Pesticide used |
2.5 Gallons Cleaning Solution |
Instructions |
Insecticides (1) and/or fungicides. |
1 Tbsp. powder detergent (2) |
Agitate, flush, and rinse. |
Hormone herbicides, salt or amine formulations (2,4-D, Dicamba, MCPA, etc) (3) |
1/2 cup household ammonia |
Thoroughly agitate, flush small amount through system, and let remainder stand
in sprayer overnight. Flush and rinse. |
|
Or
3 Tbsp. washing soad (sal soda)
|
Same as above except let stand for at least 2 hours. |
|
Or
1/4 lb. trisodium phosphate
|
Same as above except let stand for at least 2 hours. |
|
Or
2 Tbsp. fin activated charcoal and 1-2 oz. powder detergent (2)
|
Agitate, operate sprayer for 2 minutes, let remainder stand for 10 minutes, then
flush through sprayer. Rinse. |
Hormone herbicides, ester formulations (2,4-D,brush killers, MCPQA, etc.) (1) |
4 oz. washing soda (sal soda) + 1-1/2 cup kerosene + 1 Tbsp. powder detergent
(2) |
Rinse inside of tank and flush small amount through system. Let stand at least 2
hours. Flush and rinse. |
Other herbicides (atrazine, simazine,alachlor, etc.) |
1 Tbsp. powder detergent (2) |
Rinse with clean water before and after using sudsy solution. |
(1)Organophosphate and carbamate insecticides may be detoxified by adding
household ammonia to the cleaning solution (half cup per 2.5 gallons).
(2)Liquid detergent may be substituted for powder detergent; mix at a rate to
make a sudsy solution.
(3)Caution: Since only a trace of 2,4-D herbicide can damage sensitive
plants, it may be risky to use an insecticide or fungicide in a sprayer that has
been used to apply 2,4-D.
Cleaning Granular and Dust Application Equipment
These devices must also be cleaned following use. Here are some recommended
steps:
- Remove all pesticide from the device. This may require taking it apart to be
thorough.
- Clean the inside of the hopper.
- Use sand paper or a wire brush to clean rusted parts. Paint the cleaned parts.
- Coat the inside with oil. Oil or grease the bearings.
- Thoroughly clean and oil the flow control slides or valves.
- Excess oil should be wiped off if it will contact the chemical upon
- the next use.
If a pesticide applicator uses common sense, chooses the right formulation,
the right pesticide, and the right machine to apply it, he can expect a good
pest control job.
Back to Top